Revolution in der
Kelchglasfertigung
Für den modularen Aufbau von Rundläufer-Glasblasmaschinen setzt Schlemmer Prozess Systeme kompakte Simotion Motion Controller ein. Ergebnis: reduzierte Stillstandszeiten, höhere Produktivität und bessere Wartungsqualität.
Die Idee zum Bau modularer Rundläufer- Glas blasmaschinen mit 20, 24 oder mehr autarken, das heißt einzeln austauschbaren Stationen/Segmenten, existiert schon länger. Allerdings waren bislang die technischen Voraussetzungen nicht gegeben, auf engstem Raum alle mechanischen und insbesondere die Steuerungs- und Antriebskomponenten unterzubringen. Für einen Glashersteller in Asien, der eine neue Produktionslinie für Kelchglas, bestehend aus einer 16-Stationen- Stielpresse und einer 24-Stationen-Blas-Blasmaschine benötigte, hat ein bayerisch-österreichisches Firmentrio eine technisch und wirtschaftlich gelungene Lösung entwickelt. Diese Lösung für die erste modulare Rundläufer-Glasblasmaschine der Welt wurde von den Unternehmen Forma Glasmaschinen GmbH aus Neukirchen/Enknach, der Deggendorfer Schlemmer Prozess Systeme GmbH sowie der Faschang Werkzeugbau GmbH aus Weng im Innkreis (Österreich) in kurzer Zeit realisiert. Die Softwareentwicklung wurde mit F&E-Mitteln über ZIM (Zentrales Innovationsprogramm Mittelstand) gefördert.
Mit neuester Automatisierungstechnik schnell zum Ziel
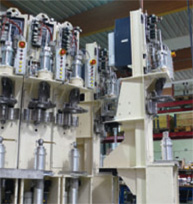
Heribert Schlemmer, Geschäftsführer der SPS GmbH: „Größte Herausforderung war es, alle Steuerungs- und Antriebskomponenten für die Drehbewegung von Blas- und Servohubstation sowie für die Hubbewegung der Servohubstation in einem Schaltschrank im Segment unterzubringen. Bei einer nicht sofort behebbaren Störung kann das betroffene Segment schnell aus dem Prozess genommen und durch ein funktionsfähiges ersetzt werden.“ So konnten die Stillstandszeiten und der Ausschuss minimiert und die geforderte Ausbeute von bis zu 40 Stück pro Minute (artikelabhängig) erreicht werden.
Mit dem neuen Simotion D410 PN für Einachsanwendungen wurde ein modularer, leistungsfähiger und kompakter Motion Controller für die präzise, feinfühlige Servoregelung des Hubs in der Servohubstation und die Vorgabe des Blasdrucks gefunden. Aufgeschnappt auf ein Powermodul PM340 des Antriebssystems Sinamics S120 beansprucht das Gerät nur wenig Einbauraum, sodass im Schaltkasten genügend Platz blieb für zwei Umrichter vom Typ Micromaster, Terminalmodule, Spannungsversorgung und Peripherie.
Höhere Verfügbarkeit durch optimierte Wartung
Damit war erstmals die Segmentbauweise möglich, die die Wartung erheblich vereinfacht. Schnellkupplungen für Luft, Wasser und Schmierung sowie Steckverbindungen für die Stromversorgung und die Kommunikation an den dezentralen Schaltkästen ermöglichen einen Segmentwechsel in weniger als fünf Minuten, der von einem dafür geschulten Produktionsmitarbeiter ausgeführt werden kann. Erleichtert wird der Wechsel einzelner Komponenten auch dadurch, dass alle Komponenten des Antriebsverbandes über den digitalen Systembus Drive-Cliq kommunizieren und alle Einstellungen auf einer CF-(Compact Flash-)Card gespeichert sind. Ein weiterer Vorteil ist die Austauschbarkeit der quasi standardisierten Segmente zwischen mehreren Blasmaschinen, in einem gewissen Rahmen auch zwischen Maschinen mit mehreren oder wenigeren Stationen. Auch auf dem Turm gibt es nun keine Komponente mehr, die nicht innerhalb weniger Minuten gewechselt werden könnte, was die Wartbarkeit im Vergleich zu zentral aufgebauten Maschinen weiter verbessert. Auf mindestens fünf Prozent beziffert Rudolf Bernroitner, Geschäftsführer der Forma Glas GmbH, die jährliche Produktivitätssteigerung seiner neuen, modularen Maschinengeneration.
Schnelle Vernetzung via Profinet
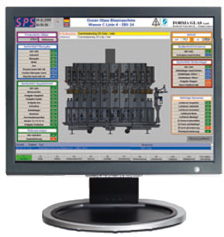
Die PN-(Profi net-)Variante der Simotion D410 ist mit zwei Profi net-Ports ausgestattet, worüber alle 24 Stationen in Echtzeit (Profinet RT) mit einer als Master fungierenden Simotion D445-1 kommunizieren. Dieser „High Performance“ Motion Controller ist im Turmschaltschrank installiert und über Schleifringverbindungen per taktsynchronem Profi bus und Industrial Ethernet mit einer weiteren Simotion D445-1 im Hauptschaltschrank am Boden verbunden. Über diese beiden Controller werden Rezepturen und Soll-Daten zu den einzelnen Stationen verteilt und umgekehrt Ist-Daten und Prozessmeldungen ausgetauscht und zentral visualisiert. Der am Boden installierte Controller koordiniert darüber hinaus die Servoantriebe und somit das Zusammenspiel von Tischantrieb, Feeder-Maschine, Entnahme, Übergabe, Vorpressen, Umsetzer und Stieleinleger.
Als zertifizierter Siemens Solution Partner Automation für Motion Control-Lösungen kennt und nutzt die SPS GmbH das Simotion System seit mehr als vier Jahren. Programmierer Andreas Lindhuber hat auch hier sämtliche Funktionalitäten ausgereizt, um die genannten Anlagenteile aufeinander abzustimmen und einen schnellen, harmonischen und dabei flexibel veränderbaren Prozessablauf zu realisieren. Darüber hinaus hat er den Systemvorteil integrierter PLC-Funktionen der Simotion Familie genutzt und auch die Ablaufsteuerung im Motion Controller realisiert. Dadurch wurde eine überlagerte SPS und damit Kosten eingespart.
Außerdem wurde eine automatische Erfassung und Einstellung der Formbodenhöhe jeder Station eingesetzt. Das ermöglicht den Einsatz nachbearbeiteter Formen ohne manuelle Anpassung und minimiert die Ausschussquote. Das Maschinenkonzept erlaubt ferner den Einsatz einer Doppel-Übergabe- und Servopressstation, sodass auch deutlich höhere Schnittzahlen bewältigt werden können, sofern es die Produkte erlauben. „Durch die hohe Leistungsdichte moderner Steuerungen können wir in Zukunft noch sehr viel einfacher und kostengünstiger auf spezifi sche Kundenwünsche eingehen“, so Rudolf Bernroitner vorausschauend, „sei es bei der Einbindung weiterer Zusatzaggregate oder einfach nur bei der individuellen Gestaltung der Bedienoberfläche.“
Komfortablere Bedienerführung
Der zweite Schwerpunkt der Weiterentwicklung zur modularen Maschine zielte auf eine noch komfortablere Bedienerführung und eine weiter verbesserte Prozesstransparenz. Voraussetzung dafür war, dass über die schnellen Bussysteme große Datenmengen übertragen werden können. Unter Simatic WinCC flexible wurde eine mehrsprachige Bedienoberfläche entwickelt, die komfortabel durch den gesamten Prozess führt. Der Betreiber kann einmal optimierte Einstellparameter für ein bestimmtes Produkt als Rezeptur abspeichern und darin auch alle erforderlichen Nebenaggregate dokumentieren. Das verkürzt nicht nur das Einstellen im Wiederholungsfall deutlich, sondern ermöglicht es auch, die Stationen mit bis zu fünf verschiedenen Rezeptursätzen zu betreiben. Stand der Technik ist auch ein Fernzugriff via VPN-(Virtual Private Network-)Tunnel, falls das Wartungspersonal einmal Unterstützung brauchen sollte oder Updates einzuspielen sind. Das spart zeit- und kostenintensive Serviceeinsätze vor Ort und hält die Personalkapazitäten des Automatisierers für andere Aufgaben frei.
Modularität mit Vorteilen in allen Lagen
Der modulare Aufbau wirkt sich nicht zuletzt positiv bei Versand und Inbetriebnahme aus: Der Maschinengrundkörper lässt sich getrennt von den Blasstationen verpacken und verschiffen, wodurch sich die Kosten verringern. Und auch die Inbetriebnahme wurde signifi kant verkürzt, indem die erste modulare Maschine bei Faschang komplett aufgebaut, per Laser vermessen, im Trockenlauf getestet und vom Betreiber abgenommen wurde. So müssen die Segmente nur noch vor Ort wieder eingehängt, angeschlossen und nochmals kurz überprüft werden. Überhaupt sind alle Beteiligten vor der ersten Inbetriebnahme beim Endkunden überzeugt davon, dass die neue, modulare Maschinengeneration die hohen Kundenanforderungen erfüllen und sich nach der Premiere in Asien auch auf dem Weltmarkt etablieren wird.